The ceramic membrane flow channels are coated with a layer of what looks like regular paint. This coating provides all the desired properties of a ceramic membrane. This coating layer may contain the ultra-hard silicon carbide material, providing high mechanical strength and durability. Let us dive into the details of what the membrane coating does and how it is made.
What does the membrane coating do?
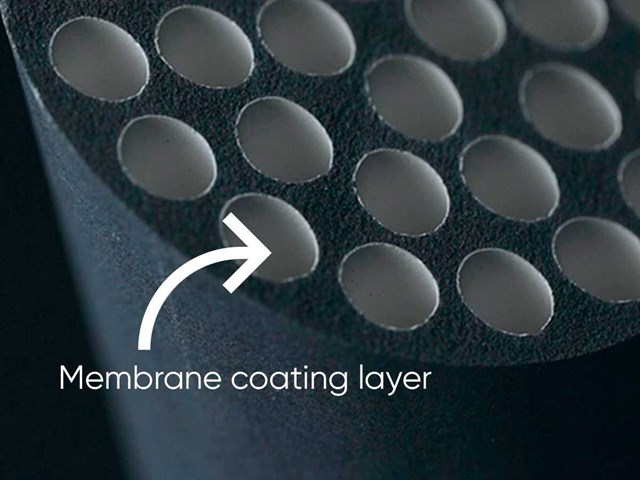
The Membrane Coating
Membrane coating, also called the active layer or the separation layer, is crucial. It delivers and controls the desired membrane properties, such as high porosity, high flux, and high selectivity, with the correct pore size and a high level of mechanical strength. The coating is usually made of an inorganic material such as alumina, silicon carbide, zirconia, or titania. Membrane coating is a layer of a colloidal suspension placed evenly on the porous support structure.
The layer must be placed evenly within the membrane support. If it is not managed to put an even membrane coating layer, it will lead to inhomogeneity, which results in uneven porosity and roughness on the membrane surface. This will make different parts of one membrane layer perform differently. Therefore, obtaining high-quality and high-performing membrane layers is critical to meet the demands of various harsh and arduous industries.
At LiqTech, we have more than 20 years of experience producing ceramic membranes, enabling us to obtain outstanding consistent coating results.
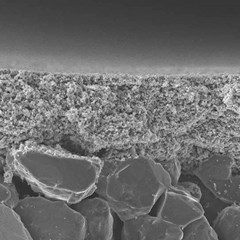
The Coating Materials
Our unique membrane coating material contains ultra-hard silicon carbide powder based on more than 20 years of experience. Learn more about silicon carbide and its advantages here.
In addition to the silicon carbide powder, dispersing agent, binder, defoaming agent, and plasticizer can also be used on the coating suspension as raw materials.
Since these materials change the coating suspension’s rheological properties, it is essential to add the right amount. For example, if the coating material’s viscosity is changed, it will lead to changes in the thickness and uniformity of the membrane layers. A high density level delivers thicker membrane layers, which will heighten the likelihood of defect formation on the surface of the membrane. On the contrary, a low density level provides silicon carbide particles’ infiltration within the membrane macropores of membrane support. Therefore, obtaining the correct silicon carbide coating suspension formulation is crucial to reach the membrane layers’ perfect morphology.
A scanning electron microscope (SEM) can see the silicon carbide support and the membrane layer can be seen in a scanning electron microscope (SEM). It is called asymmetric when the ceramic membrane consists of multiple layers with a gradual decrease in pore size description from the support to the membrane layer.
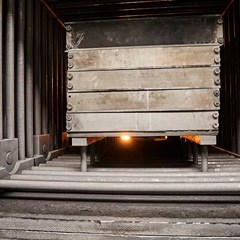
Silicon Carbide Membrane Fabrication Process
The silicon carbide membrane coating fabrication consists of multiple steps. But basically, these can be summed up in four overall steps, being:
- Preparation of colloidal suspension
- Extrusion
- Coating
- Sintering the membrane layer
Preparing the homogeneous suspension of silicon carbide powders is crucial in the first step. This is because the fabrication of the desired membrane relies on the complete dispersion of SiC particles in the solvent.
The SiC mix is extruded to the correct shape and cut at the right length in the second stem. This should be done when the suspension is wet to obtain even the most complex membrane support structures.
In the third step, the prepared suspension coats the membrane support using coating techniques such as dip-coating or spray coating.
In the fourth and last step of the silicon carbide membrane fabrication process, the membrane layer is sintered at extremely high temperatures, up to 2100 °C, under an inert atmosphere. The high sintering temperature adds to the high manufacturing costs of ceramic silicon carbide membranes. Still, a high sintering temperature is necessary to achieve a silicon carbide ceramic membrane’s desired physical and chemical properties. Click here to learn more about how a ceramic membrane is made.
Overall, the silicon carbide membrane fabrication process provides a solid adherence to the membrane support and adds robustness and durability to the membrane layers. This ensures high-quality silicon carbide membranes with extremely long service life.
You might also be interested in...
See our ceramic membrane solutions
Talk to a Membrane Expert
Do you need more information about Liqtech membranes, please do not hesitate to contact us.